Summary:
Among the most common and versatile of all the plastic cap forms, the Neck finish cap mold is used for manufacturing a...
Among the most common and versatile of all the plastic cap forms, the Neck finish
cap mold is used for manufacturing a wide range of different products, from a plastic water bottle to a plastic cap for a helmet. The Neck finish cap mold is also a great alternative for manufacturing a cap that doesn't require an outer skirt, which is often necessary to keep dirt and dust out of the cap.
History of the HDPE cap
Whether your beverage of choice is carbonated, non carbonated, or a combination of the two, a high density polyethylene (HDPE) neck finish cap may be just what you're looking for. With their strong construction, flexibility, and resistance to chemicals, they are the perfect choice for any liquid product. They are also the perfect packaging for foods, vitamins, and pharmaceuticals.
Alternative embodiments of the cap without an outer skirt
Various alternative embodiments of the neck finish cap without an outer skirt are provided. The alternative cap can be used with a variety of different cap designs and may include the following features:
The neck finish cap can be adapted to a wide variety of container designs, including blow molded bottles. For example, the threads of the cap can be modified to prevent the threads from traversing the parting line of a blow molded bottle.
The alternative cap includes a tamper-evidence band with a plurality of downward depending teeth located on the inside of the tamper-evidence band. The ratchet teeth are interengaged with the lower skirt during initial downward movement of the cap, but are not engaged during rotation of the cap. This provides tamper-indication, and prevents the cap from twisting or rotating while on the neck.
The neck finish cap may also include a tamper-evidence tear band with a plurality of radially spaced bridges connecting the shoulder and upper skirt portion. The tear band may be simulated by a continuous thinned tear line or a circular arc tear line.
Seal surfaces of the present invention
BACKGROUND OF THE INVENTION The present invention relates to a screw cap that is tamper-evident and reliable. The invention comprises a double-seal plastic screw cap that can be produced economically and provides reliable sealing under various conditions. The cap is adapted for use with a conventionally configured container. It is preferably molded in a polypropylene plastic formulation that has the desired stiffness and resilience.
The cap may be inserted into the neck of the container and tightened to a sufficient torque to ensure sealing. The cap may be tightened with a torque from 240Ncm to 600Ncm. It may also be desirable to maintain the cap's closure during everyday use and to prevent deflection during tightening.
The cap may have an inwardly raised annular bead 32. It may also have thin walls that extend upwardly from the bead to the top wall of the cap body. The bead is intended to act as a seal in conjunction with the neck finish.
Method of manufacture
Typically, a blow molded neck finish of a blow molded plastic bottle is an inward directed thin flexible flange. The sealing surface is smooth and contains no rough edges. The neck can be formed in a number of different ways. Some examples include a snap on cap or an insert for the neck. Other examples include an integrated handle.
A conventional blow mold may be used to form a blow dome above the neck finish. This conventional trim operation may also be used to shear the blow dome from the neck finish. The blow dome may be cut off from the neck using a shear insert or a separate machine.
Another form of present invention involves a widening mold. This process can be used to produce thicker wall parts and more efficient parts. This process can also be used to produce a neck finish with a different sealing surface.
A blow pin 86 m is used in the process of the present invention. This pin is diametrically fitted to a set of shear steels positioned within a split mold. The blow pin is then forced down on a striker plate 156. The pin separates the neck from the parison at a cut line. It is also possible to form the neck finish using pull-up trim.
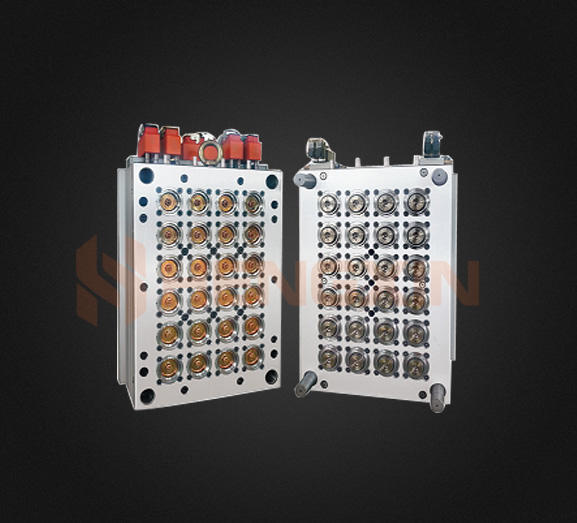