Summary:SPOON MOULD is a moulding procedure that provides durable, strong and flexible plastic moulds for high quality, precisio...
SPOON MOULD is a moulding procedure that provides durable, strong and flexible plastic moulds for high quality, precision packaging. These high quality and durable plastic moulds are perfect for creating a wide variety of objects ranging from everyday household goods and appliances like cups and plates to heavy industrial and commercial products as well. These moulds offer many advantages over conventional plastic moulds. They are environmentally friendly, reusable and cost effective. They can also offer a wide range of benefits like low density production and cost control and higher product life-span.
In general, it is quite easy to manufacture a spoon mould. However, the process requires certain skills and expertise. The main components involved in the manufacturing of a plastic injection mould for spoon shaped items are: the mould, the injection pump, the clamping system, a machine for freezing the material and an appropriate environment. Let us take a detailed look at each of these components.
SPOON MOULD consists of two parts - the mould and the clamping system. A mould is a solid body that is filled with a composition or liquid, such as Polystyrene, that will undergo the plastic injection moulding process. The mould is typically made out of steel and plastic. Clamp systems hold the mould closed and allow it to be opened for varying degrees. Depending on the type of product, the mould may either be held in one position for continuous freezing or may be opened at fixed angle intervals to allow a gradual freezing process.
Hot runners are used to inject the desired amount of melted plastic into the mould. The process of manufacturing a hot runner starts with the injection of the material into the mould. The mould is then cooled down while inside the machine is heated up to about 150 degrees Celsius. This allows the plastic to harden gradually, thereby creating the desired spoon mold. The mould is subsequently cooled down and removed from the machine.
Delivery time and complexity of the mould design are determined by several factors. SPOON Moulds with low delivery time are generally smaller in size and have lower production volume. SPOON Moulds with greater production volume require a shorter cooling-down period. Certain plastic injection mould designs also have higher acceptance levels and can be shipped overnight, which further boosts its acceptance.
Different tools are used in SPOON MOULD production. Large polystyrene sponges are used to create the moulds. A very small polystyrene wedge is attached to the bottom edge of a sponge to form a loop. After the loop is formed, it is fed into the mould. A mould release mechanism forces the plastic into the mould, where it is held for about fifteen minutes while it hardens. After hardening, the mould is removed, the polystyrene edge is trimmed, and a fresh mould is used to create another round of SPOON Moulds.
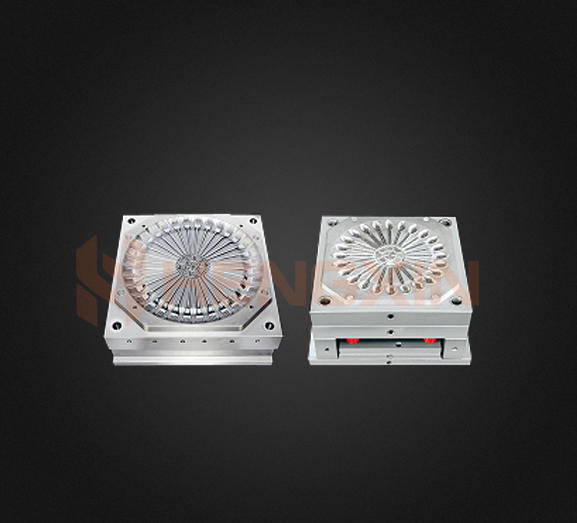
The process described above is only one way how SPOON MOULD is created. As mentioned earlier, plastic injection moulds are a popular way of creating these small SPOON moulds. These moulds are available in different shapes, sizes, and depths. It is possible to cut any pattern into any type of plastic using a knife mould tool. This allows custom manufacturing of any type of plastic. There is no limit to what you could produce, but it would take a lot of work and patience to create something special.
To conclude, there are many advantages of using plastic spoon mould molds. They are fast, inexpensive, reusable, and can be customized to create numerous different pieces of equipment. A hot runner can help cut down manufacturing time and save money. There is also the added benefit that molds can be used for other types of equipment like hot runners and knife moulds, making it a versatile tool. Whether it is a knife or an injection mould that you want to make, SPOON MOULD can give you great results.