Summary:
Injection moulding is a manufacturing process in which molten material is injected into a mould. The process can be us...
Injection moulding is a manufacturing process in which molten material is injected into a mould. The process can be used to create a wide range of products from metals to glass, elastomers to confections. It can also be used to create a variety of parts from a variety of thermoplastic polymers.
PPAP
The process of creating a PPAP injection mould involves two parts that are tightly pressed together. The mould is then filled with the polymer and heated. The material is then poured into the plasticizing screw. The rotation of the screw softens the pellets, which are then transformed into molten plastic material. The plastic material is then stored at the front of the mould, ready to be injected.
PPAP is a common process used by injection molders to ensure that new parts meet specifications. It helps manufacturers avoid costly mistakes and promote quality. It also establishes clear lines of communication between the customer and manufacturer. It helps both parties understand the steps of manufacturing before the production process starts.
Material selection
If you are going to manufacture plastic products, it is very important to choose the right material for your mould. There are hundreds and thousands of different types of plastics available, and choosing the correct material for your mould is a vital part of manufacturing successful plastic products. The most common plastics used for
injection moulding are ABS and polycarbonate. ABS is very popular due to its low cost and high structural strength. Polycarbonate is also a good material if you want your products to be transparent and heat resistant. Another high-performance plastic that can be molded is Ultem. It is often used in aerospace and medical applications.
Each type of plastic resin has distinct properties. Understanding these properties will help you choose the best material for your mould. Some plastic resins are more expensive than others, so it is imperative to know which type is most appropriate for your needs. Polypropylene, for example, has excellent insulation properties, but is flammable. Low-density polyethylene, on the other hand, is inexpensive and flexible. It also offers excellent resistance to chemicals and moisture.
Set up costs
Set up costs for an injection mould include time and labor associated with the design of the mould. Developing a mold involves the correct application of critical design elements such as drafts, fillets, gates, and ejector pins. This process can be time-consuming, particularly when the geometry of the mould is complicated. Setup fees also include labor required to mount the mould in the molding machine and calibrate the operation.
The process of designing and building an injection mould involves several different variables, and it is important to understand these factors to get an accurate estimate of the costs associated with the process. Each of these factors will contribute to the final cost of the mold.
Environmental impact
Injection moulding is a large-scale process that produces plastic parts. However, it is not without its environmental impact. The moulding process produces high levels of electricity. In order to reduce the amount of electricity used, there are several steps that can be taken. Some of these steps involve minimizing the amount of packaging material.
Using plastic instead of steel helps reduce energy consumption. There are also new materials and processes that make plastic lighter and more durable. In addition, the use of plastic insulation materials helps save energy. In addition, the use of biodegradable plastic bags makes recycling easier. Lastly, the injection moulding process is constantly being improved to make it more energy-efficient.
The study's results are consistent with other studies. The cost of the mold itself was estimated to be between US$18,760 and US$51,00. The factors contributing to the high upfront cost of the mold were labor costs and expensive AM raw materials. The study also showed that the lead time to manufacture a single mould in the U.S. was 6.7 weeks. This was 22% faster than in China. The study's findings correlate with manufacturer surveys and government reports.
Production part approval process
Injection moulding companies have to follow the Production Part Approval Process (PPAP) to ensure the quality of their products. This process was originally created for the automotive and aerospace industries and provides standardized guidelines for manufacturability. It specifies whether a part can be consistently produced during normal production runs and at defined production rates. Its goal is to ensure that parts are produced to specification and prevent defective parts from reaching the end user.
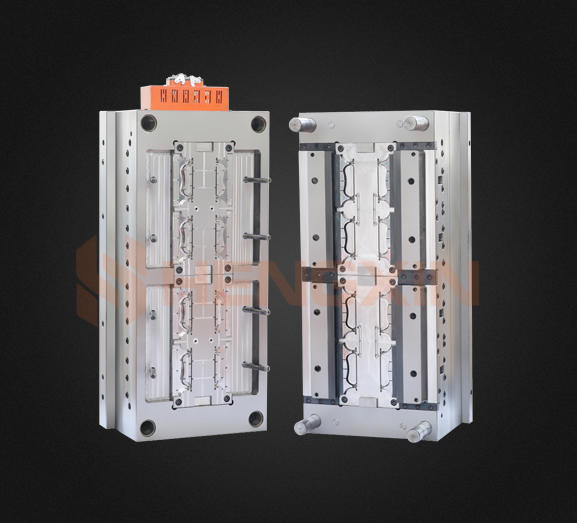
This process ensures that the first products produced from a new mould are safe and of the highest quality. Any flaws or inconsistencies found during the process will be resolved immediately. The process involves comparing the required dimensional specifications of a product with the molded version. Any flaws found during the process are immediately corrected, and the process is repeated if necessary.