Summary:
The process of plastic household moulding involves putting a resin or liquid into a mould. The mould is then rotated a...
The process of plastic
household moulding involves putting a resin or liquid into a mould. The mould is then rotated at high speeds until the liquid covers the entire surface. The plastic then cools in the mould to form a hollow object. The finished object is then removed from the mould. This process is highly efficient and environmentally friendly. It is generally used for large hollow parts.
Injection moulding
The process of plastic household mould injection moulding begins with the design and creation of the plastic mould. The design will be based on a variety of criteria, including the material, fillers and resin type. The cost of the mould will depend on the material used, but it will also be influenced by the cost per unit weight. The thickness of the plastic part will also determine the amount of material needed. The amount of material also depends on the design of the mold and the size of its channels. Once the mould is ready, it must undergo post-processing to recycle the thermoplastic trimmings. This process involves using a plastic grinder, also known as a granulator, to grind the thermoplastic trimmings into pellets. The pellets produced are then mixed with raw material, in the proper regrind ratio.
The injection moulding process can produce many different types of plastic parts for a variety of applications. The most common plastic product manufactured each year is plastic bottles, which are made from polyethylene terephthalate (PET). This material is remarkably strong and lightweight. Plastic moulds are also used to make electronic housings, such as those found in remote controls, computers, medical equipment, and more. This process allows manufacturers to create custom plastic enclosures for virtually any application.
Rotomoulding
Rotomoulding is a process that involves inserting powdered resin inside a hollow mold and rotating it slowly. The material slowly melts inside the mold, coating the inside walls. The molds are designed to rotate biaxially, ensuring a uniform distribution of the resin throughout the part.
The process is economical and efficient for low-volume production. It is versatile and can accommodate complex shapes, stiffening ribs, moulded inserts, and a variety of surface textures. Moreover, rotomoulding can produce parts with consistent wall thickness, which increases the strength of the finished product.
The molten plastic must be thermally stable to be used in moulds. Otherwise, the melted plastic may oxidize and lose its properties. Therefore, the plastic must contain sufficient antioxidant molecules. In addition, it must be able to flow easily through the cavity of the mould. The flow characteristics of the plastic used must also be considered when designing the part.
Hot runner systems
Hot runner systems are injection molding systems that use heated channels in the mould to supply molten plastic to the part. The temperature of the molten plastic is controlled to achieve the desired results for the part and the injection process. The hot runner systems are designed with different types of nozzles and manifolds that control the flow of molten plastic. Manifolds can be designed in various shapes and sizes and are made from a variety of materials. There are two main methods for manufacturing manifolds. Gun-drilled manifolds are used for a simpler and more economical system, while two-piece brazed manifolds are used for more complex and performance-oriented systems.
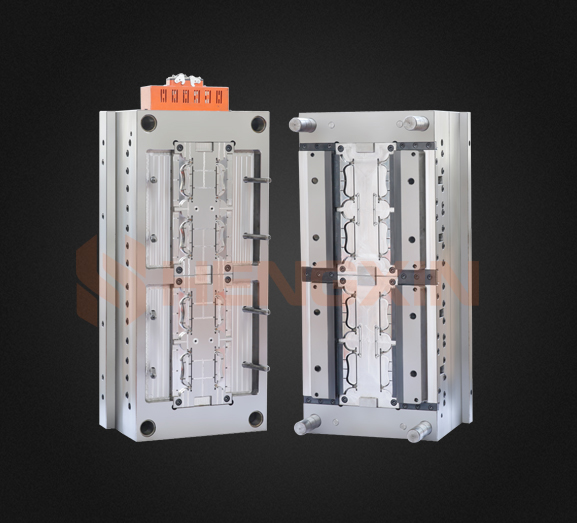
Hot runner systems reduce mould cycle time and reduce plastic waste. However, they increase mould manufacturing costs and are more difficult to maintain. They also have problems with clean-up because the runners are hidden and it is difficult to remove leftover plastic. In addition, the heat generated by the hot runner systems can be difficult to control and can cause sticking problems, particularly with thermally sensitive materials.
Mold release agents
When it comes to removing plastic household mould, silicone mold release agents can help you. They are designed to be easily removed with soap or a mild solvent. The silicone releases the mould without damaging the plastic. But be aware that oil can pool in fine details of the mould. You can always use a paper towel to absorb any excess oil.
Release agents help prevent other materials from bonding with the mold surface. They also help with the removal of the cured part from the mould. Various household products are available for use as release agents. These are generally less expensive than specialized mold release agents.
Quality control
Quality control is an essential component of molded products. Failure to meet this standard can result in a faulty product. Several factors can contribute to mould quality issues. For example, poor mold maintenance or design can lead to mold parts with imperfections. This can result in a costly overhaul. To avoid such problems, proper quality control should be practiced throug