Summary:The first step in building a preform mould is to choose the size of the preform. The diameter of the mould should be aro...
The first step in building a preform mould is to choose the size of the preform. The diameter of the mould should be around six inches, but it can be as large as twelve inches. The final preform size should be at least half as big as the final product. Moreover, the screen should be sized appropriately. Ensure that the thickness is a reasonable value. The preform height must be just right.
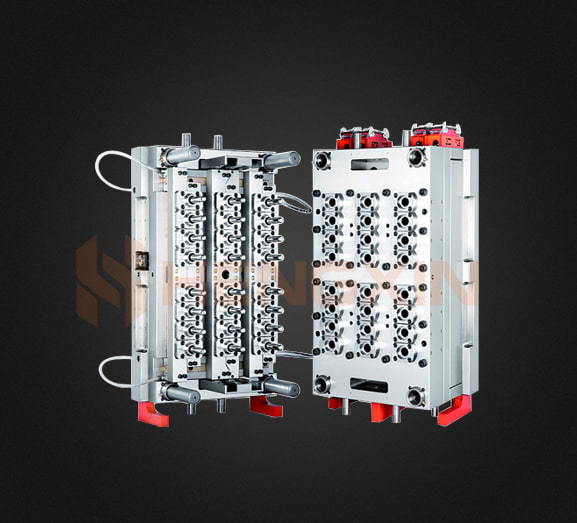
The preform mold should be made of plastic with a high level of strength. It should be durable. It should be easy to clean. Besides, it should have a high level of quality. The materials should be easily available in the market. It should be polished and have anti-rust features. The material should also be competitively priced. The quality of the finished product will depend on the design of the mould. If the plastic is a thermoset, it must have a good surface finish.
A PET preform mould should be designed for the LingMA injection molding system. The self-lock mold is suitable for making small batches of bottles. The valve gated preform mould is ideal for small quantities. Both the sides of the PET preform mould are made of a single material. There is no difference between these two types. The self-lock mold has more cavities, while the non-self-lock mould has more.
Various types of preform moulds are available. Several types are self-lock and non-self-lock. The self-lock preform molds are self-lock. A non-self-lock mould is a sandwich between the two materials. Both moulds can be designed in accordance with the customers' specifications. They can be customized according to the specifications and requirements. The PP and PET preforms are available.
A preform mould is essential to make PET bottles. If you want a high-quality bottle, you should choose a quality mould. A high-quality mould is a key component in the manufacturing process. A PET mould should be well-designed to prevent leakage. The preform should be resistant to breakage and be highly resistant to chemical agents. If the bottle has a handle, it can easily be handled. Its design is also an attractive feature.
The main components of a PET preform mould include S136 and P20 materials. The German vacuum stove is used for heat treatment. These materials are resistant to the heat of the plastics. There are various machine tools used in a pet mold. A PET bottle preform mould should be able to withstand high pressures. They should also be designed to reduce the possibility of leaking or breaking. The design procedure of a custom-made perform are based on a customer's needs.
Another factor to consider is the amount of recycling. A Preform Mould can be used to make the final product. A good quality PET bottle is recyclable. The mould must be a good fit for the material. When using plastics, the material should be as light as possible. The preform must be compatible with the machine. For example, it must be lightweight. However, a custom-made bottle may be more expensive.
The design of a preform mold is crucial in making a quality product. A mould is not complete without the necessary details. A proper design should allow for maximum flexibility. A preform mould should not only be functional, but also aesthetic. It should have a unique look that makes it stand out from other plastic products. It should also have a smooth shape. The mold should be a sturdy and stable structure. When using a custom-made plastic, it should be durable.
A preform mould can be used for making bottles. The mold should be sturdy and stable. A good mold will not break easily. The material should be durable. It must be reusable. A high-quality bottle mould should be durable and versatile. A good mold will not need to be expensive. A good one is a good fit for the plastic product. If you are looking for a plastic bottle, a custom-made mold should be sturdy and durable. It should also have the appropriate dimensions for the desired application.
When using a custom-made preform mould, you should be able to choose a mould that fits your specifications. It should also be compatible with any type of resin. The preform should be lightweight and resistant to corrosion. It should be easy to clean and dry. It must be durable enough to withstand temperature changes. It should be made of durable material, including plastic. Similarly, a thermoplastic material must be compatible with the material of the injection mold.