Summary:The design of a plastic injection mold for a crisper cover would involve creating a mold tool with the shape and feature...
The design of a plastic
injection mold for a crisper cover would involve creating a mold tool with the shape and features of the desired cover. This would typically be done using computer-aided design (CAD) software, and the mold would be made of steel or another durable material. The design should take into consideration the type of plastic material that will be used, the size and shape of the cover, and any features such as snap-fit connections or textured surfaces. Additionally, the mold should be designed to be easily maintained and have a long lifespan. Finally, the design should be validated with simulations and test runs before mass production.
Plastic injection molding is a manufacturing process in which molten plastic is injected into a mold and cooled until it solidifies into a specific shape. It is used to produce a wide variety of plastic products, including the crisper cover you mentioned. The process typically involves the following steps:
Design and fabrication of the mold: The mold is created based on the design of the crisper cover, and is typically made of steel or aluminum.
Material preparation: The plastic material is typically in the form of pellets or granules, which are heated and melted in a barrel. The melted plastic is then injected into the mold.
Injection: The melted plastic is injected into the mold under high pressure. The mold is cooled to solidify the plastic and retain its shape.
Ejection: Once the plastic has solidified, the mold is opened and the part is ejected.
Trimming and finishing: Any excess plastic is trimmed away, and any necessary finishing touches are applied, such as painting or labeling.
Quality control: The finished product is inspected to ensure it meets the required specifications.
It's important to note that this is a general overview of the process and specifics can vary depending on the type of plastic and mold used, as well as the size and complexity of the part being made.
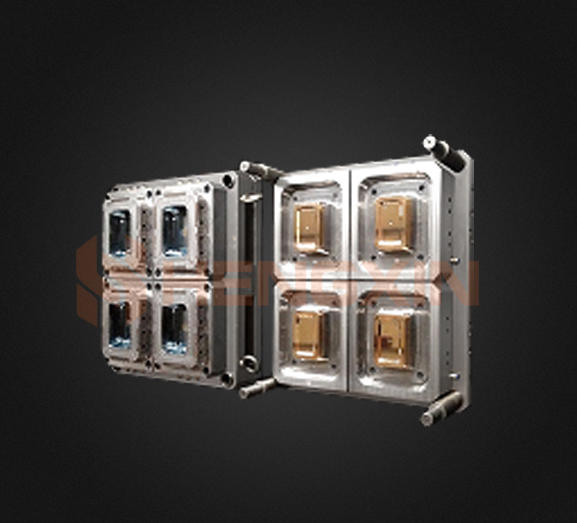